The Importance of Team Culture in the Maintenance and Reliability Industry
John-Paul Lambert
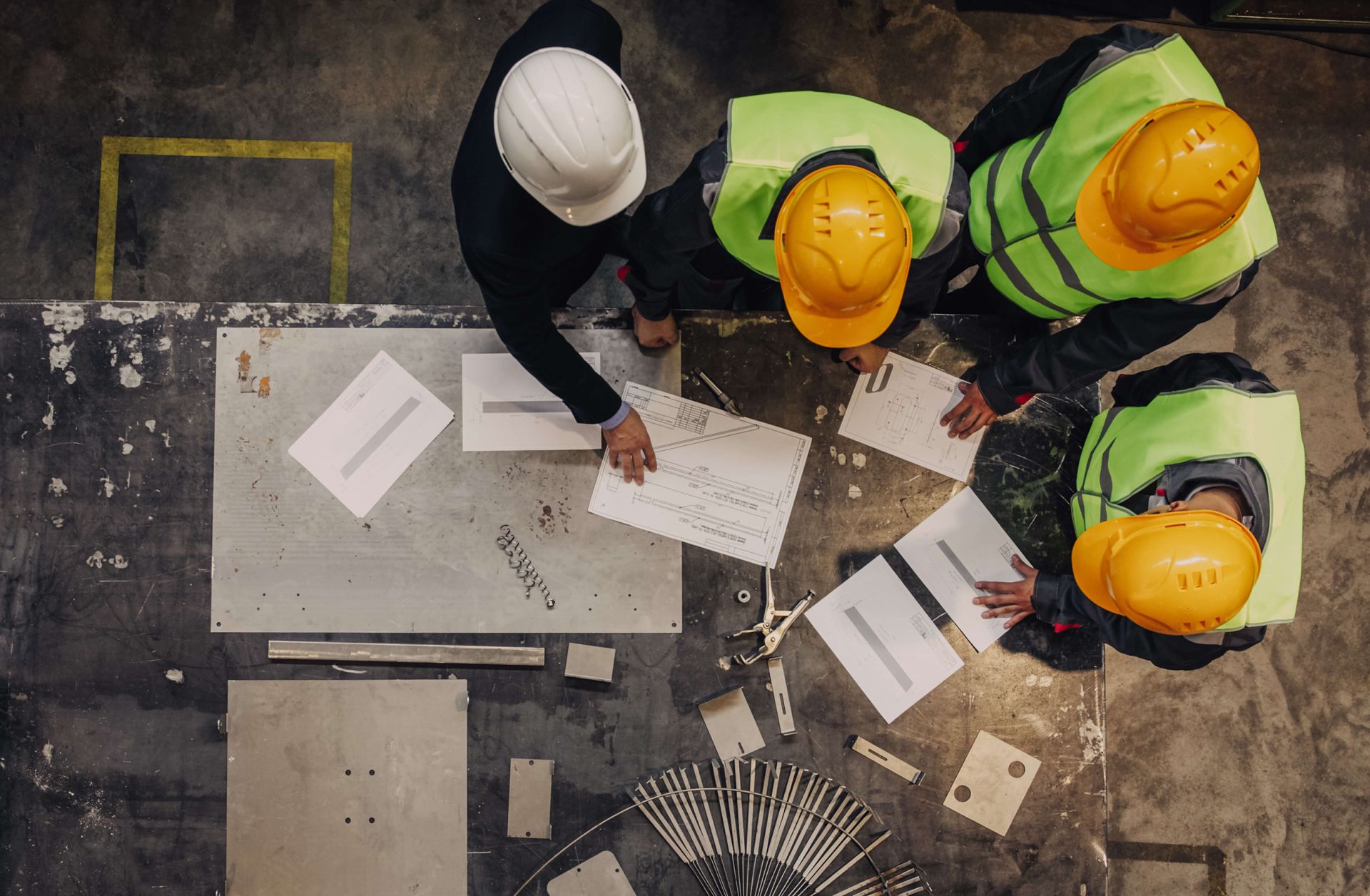
The maintenance and reliability industry is a largely technical one. In our MAAD Training Program, we know how easy it is to focus on the facts and treat the whole thing as a numbers game – after all, the first letter of our acronym stands for MEASURE.
The truth is, every workplace contains humans and that means our jobs are about more than alignment training, maintenance processes and re and re’s (remove and re-fits). In between all those hard numbers and moving machinery are very real people.
That’s why quantifiable data is only half the challenge of building a precision maintenance program.
The other half is making sure all those people are on the same page. And that means that creating a strong, positive work culture is key.
The difficulty of workplace culture clashes
Workplace culture is the behaviours, beliefs and values employees share as a group.
Most maintenance groups have at least two or three cultures, even though they are one group.
There is:
- Upper management culture – plant, production, maintenance, engineering and reliability managers.
- Middle management culture – supervisors, foremen, planners and lead-hands, these are the front-line supervisors.
- Shop-floor group culture – trades/craftsmen, millwrights, labourers and lube techs.
In some organizations, these groups can work effectively together. In others, they don’t. Instead, it becomes an “us VS them” situation.
This will hamper precision maintenance as much as ignorance or poor processes.
Maintenance VS management
During precision maintenance, machinery installation and measurement training, we too often see each as an “us VS them” scenario.
For example, it’s a rarity for front-line supervision or management to sit in on training programs, but front-line workers often view middle-management as ‘on the management’s team’. So, when the doors are closed and it’s just the tradespeople, it begins with “we just do what we’re told.” But as the day goes by, and we learn to trust each other, more of the true culture of the shop-floor group comes out.
One of the reasons we are able to attain their trust is that we share in the shop floor experience with each person we teach.
A matter of perspective
Many years ago, I was on the tools as a maintenance mechanic/millwright and thoroughly enjoyed it. I have also worked as a maintenance lead-hand, foreman, supervisor and alignment training instructor. These experiences allow me insight into the perspectives of multiple maintenance team cultures.
Like most people, tradespeople appreciate the opportunity to vent to someone who understands their issues. What I’ve found, both from my experience and from listening, is their underlying concerns are:
- They don’t feel supported
- They don’t feel listened to
- They don’t feel involved
But, my experience is not just tied to the shop floor. I also understand the concerns of the front-line supervision because I’ve been there too.
Being sandwiched between upper management and tradespeople is not easy. For example, one of the reasons upper management doesn’t sit in on alignment or measurement training is because someone might bring up a situation where a machine was not correctly repaired, yet was put back into service – which can cause friction. However, there could be several valid reasons that the machine was put (or not put) back in service.
So, while the different groups need to work together harmoniously, there will always be some separation. That means creating good working relationships when and where we can.
Who’s the boss?
Many years ago, when I was a supervisor, I met one of our shop's tradesmen and his wife out shopping.
He introduced me as his boss, but I told his wife that was not true, as, in fact, I worked for him. I said (and believed it) that my job is to get him whatever he needs to get the job done. If he needs a nut and bolt that he has forgotten to bring to the site, I get the nut and bolt for him. Why? Because he is doing what needs to get done and that’s the most important role in any maintenance department.
Now, I know some of the shop-floor guys are not angels. I have listened to the stories about what goes on and have been on many a job myself, so I know. I have listened to the griping that says “they don’t care, so why should we?”
Well, the answer to that one is pride. Fortunately, the majority of tradespeople have pride, meaning they want to do a good job.
As long as there are tradespeople with pride on the shop floor, the culture needs to go beyond leaders and workers. Like all good relationships, there needs to be two-way communication.
Building a better maintenance team with precision maintenance
Whatever your position or your culture, the most important thing is to get the job done as safely and efficiently as possible. Using the skills we have, we strive to not only maintain but to improve.
We don’t always have to like each other but if we can respect the roles we all play and share a common goal of improving maintenance processes, the culture can change for the better.
A simple way to start this is by implementing a precision maintenance program. With precision maintenance, you concentrate on ensuring failure prevention and defect elimination in the tasks performed on your machines and equipment by your maintenance and operations people.
We call it MAAD Training because it follows a simple process: Measure, Analyze, Act and Document.
The MAAD concept can be used by anyone in the maintenance and reliability industry when trying to improve maintenance processes. It’s also a method we promote and believe should be followed, whether you’re a millwright, mechanic, maintenance manager, supervisor or reliability expert involved in machinery installation.
Measurement: find a simple and effective way to measure your processes (to control a process, you have to measure it).
Analyze: as a group, ask the question “why”. Make sure you get truthful, honest answers from everyone.
Act: if necessary. Even leaving a machine as-is is an action.
Documentation: If you don’t document and you need to look back to analyze, you are only guessing as to what happened.
The best part is you can keep this process as simple as you want.
For example, you could review and measure the effectiveness of your precision maintenance program. The action taken may be to rewrite the program but whoever does the actual work should be involved with the rewrite.
Sometimes a dynamic individual or program can change the culture of a workgroup but remember, it takes a whole team to sustain it.
To move forward, we all need to work together and foster a stronger, more harmonious team culture.
Subscribe to our newsletter and prepare to get MAAD about machine maintenance.
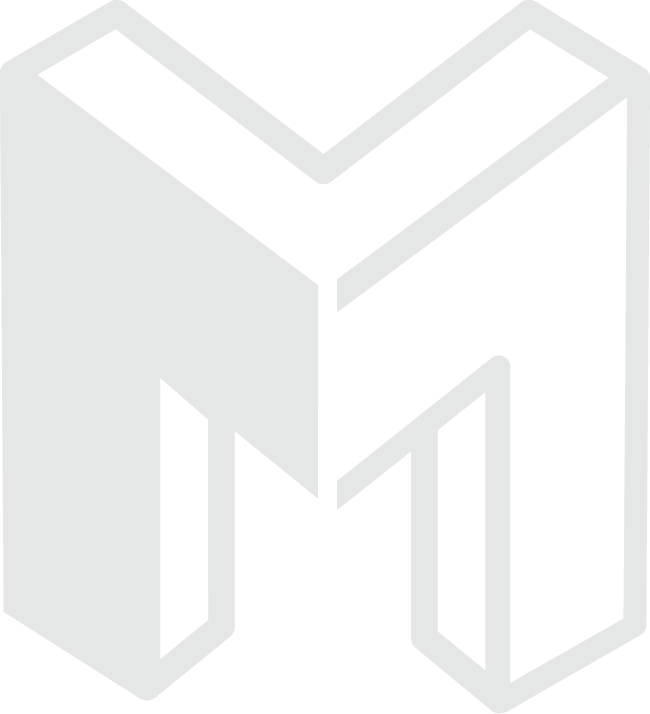
© Copyright 2022 MAAD