Five Things You Need to Know to Implement a Precision Maintenance Program Today
John-Paul Lambert
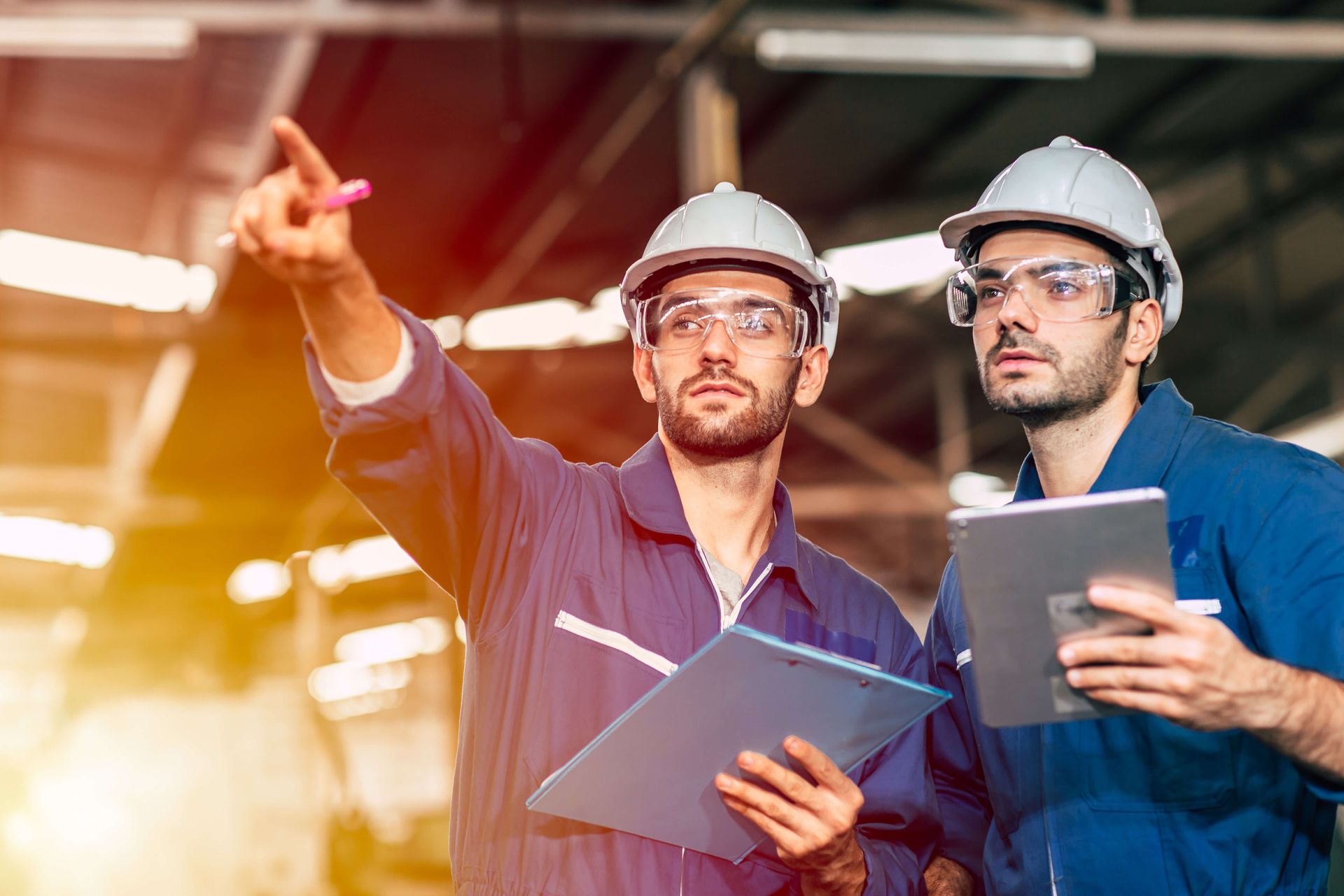
Every shop has a maintenance program that may or may not work for them.
However, the cost and energy required to change the paradigm, retrain the workers and follow through often seem very steep. So, even if a new program would be beneficial, it’s hard to convince everyone to get on board.
The good news is not only is precision maintenance an effective way to maintain your assets, but it’s also easy to implement. In fact, you likely already do most of the work already. Instead of throwing out what you do and trying to revamp your whole program, precision maintenance can be used as a process improvement strategy.
The beauty of this process is there’s not a whole lot of cost involved, and with a bit of planning, you can implement the process one machine at a time.
An introduction to precision maintenance
In simple terms, precision maintenance means working to a recognized standard, tolerance or specification. Just doing that will improve your work processes to maintain more reliable machines (assets).
It’s important to note that a ‘recognized standard’ means the benchmark is approved by an organization such as the Canadian Standards Association (CSA), the International Organization for Standardization (ISO) or the American National Standards Institute (ANSI).
That is the foundation of precision maintenance. Starting from here, all your shop needs to start implementing this maintenance protocol are five simple things.
The five things you need before implementing precision maintenance processes
1. Work Procedures
Work procedures are written documents that outline the work process. Typically, shops have them as part of a preventive maintenance program, but they are rarely comprehensive. For a precision maintenance program, work procedures need to be precise and exhaustive, covering everything from simple checks to in-depth pump overhauls. They also need to include the standard tolerances and specifications you need to do the work properly. This ensures consistency during all maintenance procedures.
If you do not have written procedures or have old, outdated ones, you need to create them – today. Though it’s tempting to find best practices online or from other sources, the best people to write work procedures are actually the tradespeople themselves. That’s because they know the work processes best. Better still, create procedures as a team-building exercise as it will create more buy-in from your crew. However, no matter who creates them, work procedures must be clear, comprehensive and easily understandable.
2. Measuring Tools
Precision Maintenance requires exact measurement. So, you need instruments that can achieve this. You need to match your measuring instruments to the tolerances. After all, you cannot have a tolerance that you cannot measure. This means you need the right tools for the job.
We always recommend using digital instruments so that the measured value or result is saved electronically. This is because when using analog instruments, such as theodolites, dial gauges or levels, the greatest error occurs during the transfer of the seen value. Our one piece of advice is: do not buy junk. You need reliable equipment for your team to use. Once again, it pays to get your tradespeople involved in choosing the right tools required so there is more buy-in.
3. Data processing system
You probably have a precision maintenance program that’s controlled by a data processing system (such as CMMS/EAM). This is essential to precision maintenance because it gives you an organized structure. In this system, there should be planned work orders, backlog orders, precision maintenance schedules, CBM tasks, etc.
To utilize it effectively for a precision maintenance program, your data processing system needs to have two things:
- An individual file for all the plant’s assets. In each file, there needs to be a benchmark record of each machine’s normal operating condition. For example, the normal operating temperature should be recorded in your system as well as where you would take those measurements from. This is simple enough to do and is so helpful for the precision maintenance technician.
- An asset history file, which includes the asset/machines installation report or a coming into service report. This is the information that controls the reliability of this machine. Imagine if you had to do a breakdown analysis after a failure and did not have this information. You would be relying on guesswork, which is never precise.
This report should include:
- Base flatness and level
- Shaft runout
- Coupling runout
- Pipe and conduit strain
- Soft foot
- Offline To Running (OLTR) machinery movement
- Shaft centerline to shaft centerline (alignment)
*All of these items and the recognized standard tolerances/specs can be found in ANSI/ASA S2.75-2017/Part 1.
With both an installation report and a commissioning report, they guarantee the machine has a good starting point when starting service. Throughout the machine’s lifespan, maintenance workers will add information to this report, such as an ‘As Found’ and an ‘As Left’ alignments, or even a base flatness change, as things inevitably move.
4. The right skill sets for the work
I had a conversation with a maintenance shop foreman who suggested that not everyone in the shop had the same-sized toolbox and that he would pick and choose who to put on what job. What he meant was that not everyone has the same skill set.
For example, I know a company that bought an expensive and not-so-user-friendly laser alignment system. The problem was that not all the shop guys could use it. It may have been able to be taken to the job site, but because not everyone could use it, chances are it won’t be used correctly or won’t be used at all.
This is one of the reasons we are developing training videos to help support some tradespeople who struggle with new technology. This way, they can take their time and review it as often as they need – especially before going out to perform an alignment job. To start implementing an effective precision maintenance program, all members on the shop floor should be proficient in taking and recording measurements. So, you may want to invest in training.
5. The right team culture
Starting a precision maintenance program is a comprehensive step that requires the whole shop to work together as a group, dare I even say a team. This can put some people off. But, in today’s industrial environment, it should be evident to all that we have to work together in order to compete.
So, my advice is to sit down collectively and ask some tough questions, such as “can we do this?” and “what do we need?” This way, you can get more buy-in from your team.
Making the leap to better maintenance
If you are in maintenance, whether management or skilled trades, embarking on creating a program like this is challenging to say the least. It is, however, a worthwhile investment that will not only build confidence in your team but also increase machine/asset reliability.
In today’s world of potential global pandemics, we’re lucky to be able to leverage scientific knowledge to help us make the best choices about our health. That’s not unlike what you do with your condition-based maintenance program where decisions are based on the measurement/data taken.
It’s the same with this program. It is data-driven and quantifiable, that is reproducible measurements are taken, analyzed and compared to a standard. Actions are taken based on this data and the whole process is documented.
For well over ten years, our training has been called MAAD which is an acronym for Measure, Analyze, Act and Document. We suggest you do something along these same lines if you want to improve your maintenance process, and quite simply, do the job right.
You’re doing the work already, why not be the best you can be?
Subscribe to our newsletter and prepare to get MAAD about machine maintenance.
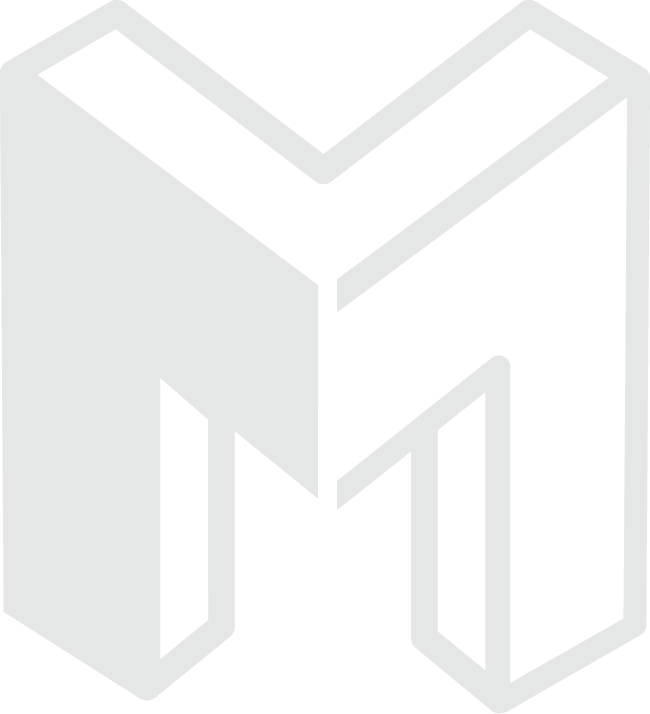
© Copyright 2022 MAAD