Condition-based Maintenance VS Precision Maintenance
John-Paul Lambert
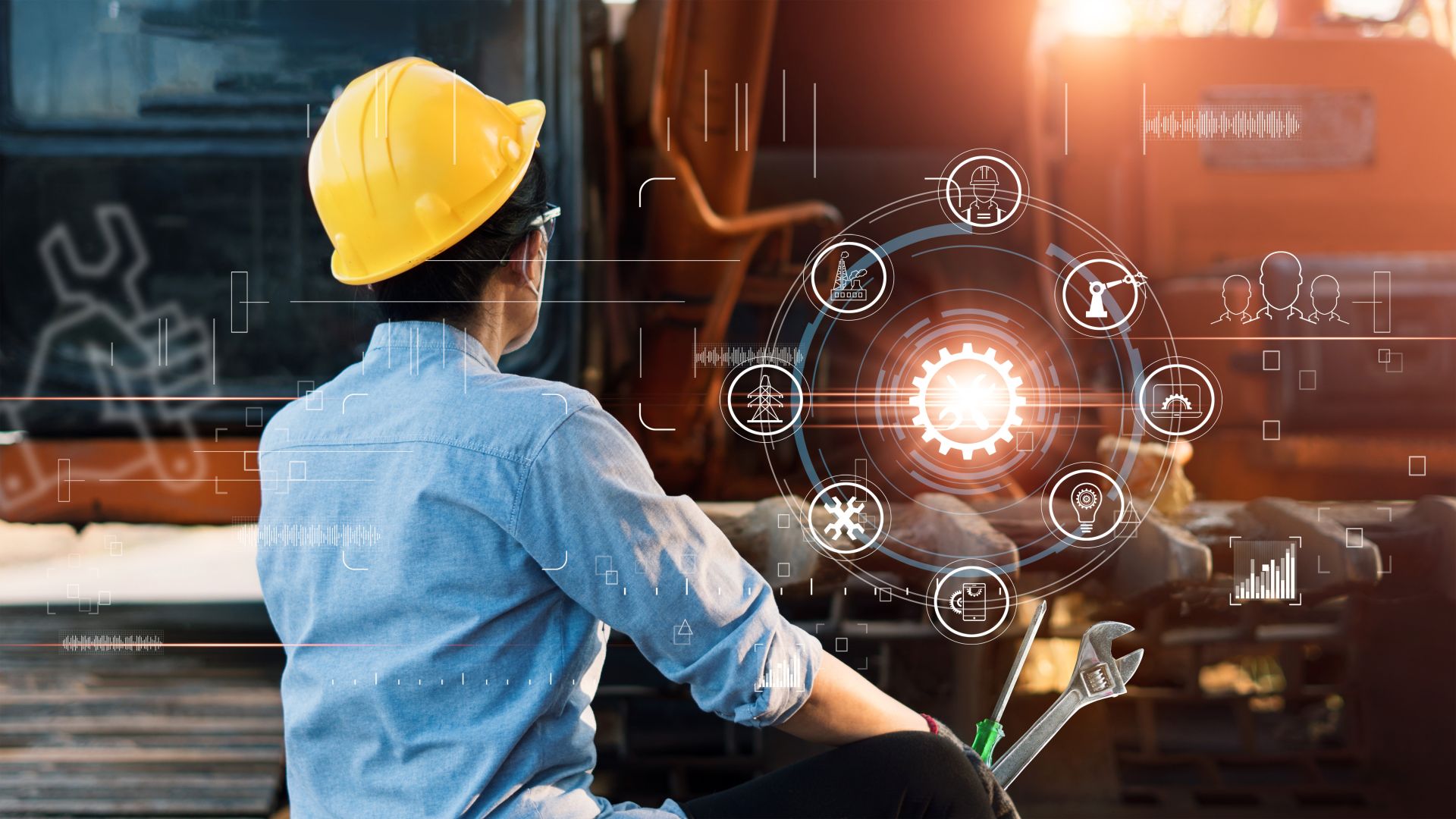
What maintenance should an organization focus on?
Recently, the P to F interval curve (explained below) has popped up a lot on my LinkedIn feed and in articles I’ve read. So, I’ve been thinking a lot about it and how it fails our maintenance teams. We were first introduced to the P to F interval curve many years ago when I was implementing reliability-centered maintenance in a plant’s engineering and maintenance department. As an integral part of condition-based maintenance (CBM), it’s an important first step to a better maintenance foundation. However, we shouldn’t stop there.You see, CBM has a major flaw. It doesn’t begin until the machine is running, which means it still allows for premature failures. That’s where precision maintenance comes in.But before we start talking about precision maintenance, let’s do a quick refresher on CBM and the P to F curve. That way, we can make sure we’re all on the same page.
The P to F curve
The P to F curve is used as a learning tool for condition-based maintenance. The curve represents the life of a machine or an asset. The ‘P’ stands for potential failure or the point when a change in the condition of the machine is detected. The ‘F’ is the point where it reaches functional failure. This means that it is not doing the job it was designed to do. That’s where CBM comes into play.
Conditioned-based maintenance
In the graph, you can see the P to F interval curve starts when the machine starts and monitoring begins. Monitoring then continues until a maintenance technician takes a quantifiable measurement that is outside the machinery’s optimum running specs, that is ‘P’. Then, before the machine runs into ‘F’, the machine is maintained.What you’ll notice here is that CBM is based on measurement, which is good. We all know that to control a process we must measure.However, the problem is, CBM misses both the design and installation of the machine. A small point but it makes a big difference, as we’ll see later.
An example of cost savings with CBM
At the plant I worked at we used ultrasound tech to monitor bearings. We detected a very early warning in the sound level, so, we greased the bearing and the sound level dropped.
Because we saved the bearing from any damage, and we saved a potential breakdown, this created a cost savings. Plus, even if there were any bearing damage, the fact that we were aware of and monitoring the situation allowed us to avoid any secondary damage on the part.
Potential failure to functional failure
Functional failure comes at us in many ways and we have many ways to combat it. In fact, just because a piece of equipment has moved from P to F doesn’t necessarily mean it won’t work. It all depends on the consequences of the failure and how its stopping/continuing affects the plant.
Consider this: If I have a bucket that has a hole in it, it is in a functional failure state. But can I still use it to bail out my sinking boat? You bet I can!
Or, say a seal designed to keep fluids in and contamination out is leaking. Though it’s in a state of functional failure, chances are, this leak won’t put the machine down. Of course, this depends on the importance of the seal and its application.
If the seal is protecting a gearbox, it would be more affordable to schedule maintenance and replace the seal than it would be to wait for the seal's functional failure which could cause potential failure in the gearbox. If we let these failures continue, it would get even more expensive – especially if we needed to replace a shaft because a bearing in the gearbox has seized onto and ruined it.
Secondary, ancillary damage can mount up very quickly if you don’t heed the warning you are given with potential failure.
The benefits of early detection and cost avoidance with CBM
If we detect potential failure early enough (which can be months and months before actual failure) it means we can avoid breakdown and ancillary damage. The earlier the detection, the more time to plan and view your options. Then, we can schedule an outage to repair the machine. So, if it’s not a breakdown, the machine hasn’t stopped – there’s no downtime. This is cost avoidance and the plant can save on the interrupted loss of production because of downtime costs. This is an important detail. ‘P’ is always a fixed point but ‘F’ is a moving point because no one knows when potential will move to functional. Not all warnings of failure put the machine down and very often you have options and time.
The failure of CBM – leaving out machinery installation
The failure of CBM doesn’t come after the P – it comes before it. The P to F interval curve graph can be extended back to the very design of each machine. Then, consultants (and I’m guilty) like to put labels on the different kinds of maintenance and where it takes place, such as:
- Design, Capability, Precision Maintenance
- CBM, Predictive Maintenance
- Preventive Maintenance
- Run to Failure, Breakdown Maintenance
Looking at this new, longer graph, we can see the original CBM graph doesn’t start until quite late in the overall arch of the machinery’s lifespan.
But, we still have premature failure. This means that CBM is no better than Predictive Maintenance. This doesn’t mean that we don’t recommend CBM, we do. It’s a must-have, but it does not improve the maintenance process because you will still have a mechanical failure.
The sunk cost of CBM
We use many predictive maintenance technologies in CBM that cost a lot of time and money to implement, like:
- Vibration
- Ultrasonic
- Infrared
- Oil analysis
- NDT (i.e. pipe wall thickness)
- Operational Performance
They’re all great technologies, and, when used in combination, they work even better.
For example, vibration may give you the most information, yet ultrasound may give you the earliest warning on a high-speed bearing. And then there is oil analysis, which may be best for a low-speed gearbox. It all depends on the application you have that will dictate what’s best for you.
As you know, CBM gets complex quickly. In most plants, a lot of time, money and effort has been spent getting the best CBM program and the right technology. With all that effort to perfect CBM, it can be hard to let go, even if the alternative saves money in the long term!
The truth about machine lifespan and failures
Machine failures fall into three categories:
- Premature failure
- Random failure
- Age-related failure
We want the latter of these, which CBM does not give us.
In fact, studies show that only 11% of machine assets fail because of age-related issues. They grow old and wear out. This means 89% fail before they should.
These numbers come from a very famous study by Nowlan and Heap that was commissioned by the US Defense Department. These numbers aren’t necessarily an exact reflection of every industry, but the study has stood the test of time and led to the development of reliability-centered maintenance.
Crunching the numbers on CBM’s short-comings
Let’s say the numbers from the study above are wrong. Let's double the numbers on age-related (full machine life expectancy) failures.
Despite the decrease, we’d still see 78% of failures in the premature or random categories. Even if we quadruple it (56% are random or premature), we are still on the wrong side of the equation.
The maintenance goal needs to be getting the full life expectancy out of all machine assets.
This is good news because it allows us to stop up to 89% of failures before they happen.
But, to get the full life expectancy for a machine unit, you have to expand that graph to include two things:
- The design of the unit, which includes all related parts (not just the pump but the piping as well)
- The installation of the unit
And CBM just can’t help us here.
Increasing lifespan through precision maintenance
There’s a reason why precision maintenance is an integral part of our MAAD Training Program.
It simply means: Working to a higher standard in machine maintenance.
Unlike CBM, which only begins after firing up the machine, precision maintenance can begin the moment you buy the equipment. From moving the machine to storing it, how we treat our new equipment affects its reliability.
But most maintenance teams don’t have control over the machinery this early on.
What is more realistic is starting your maintenance with the design and installation of the machine.
Creating optimal conditions for precision maintenance
Now, in most cases, we don’t design the pump, gearbox or compressor, but we do size them to meet the required output. And, we do quite often design the piping configuration or the bases. Ideally, this is where we should start precision maintenance.
However, that’s not always possible either, as maintenance departments typically maintain machinery that’s already in place.
So, although new installations needing design work are not often performed, installations, through remove and re-fits (re and re), are done constantly. And that installation is something we can control. In fact, it’s that installation that has the greatest influence on the machine’s life.
It’s during re and re where precision maintenance has the greatest effect in most shops. Here, the goal is to create a stress-free environment for the machine to operate – no pipe strain, no distorted bases, no thermal expansion, no misalignment, et cetera, et cetera.
A gap in equipment reliability and maintenance standards
Maintenance departments can set their own standards. However, the team all must agree on it and adhere to it. This is the only way to control the installation process and it’s. This is the way to stop random failure and get the full life expectancy from your machine assets.
The issue is, we don’t have a general machinery installation standard to work to. Yes, we can and do use guidelines from other specific industry sources – such as the American Petroleum Institute (API) or OEM specs. However, there is nothing in place for the general industry as a whole.
The good news is this is about to change. The American National Standard Institute (ANSI) has just approved a new standard which is about to be published. I know this because I worked on it and will be writing about it shortly.
Emphasizing precision maintenance
If a customer were to buy a vibration monitoring tool before they bought a laser system. I would think their focus is on the effect of the issue, not the cause. What do you think?
We cannot control the failure. What we can control is the installation. If done correctly, this will improve the process giving the optimum life for the machine.
If we look at the life cycle of a machine, we need to know and manage the failure as best we can. If we only focus (or mainly focus) on the failure, we will not improve equipment reliability and maintenance.
Subscribe to our newsletter and prepare to get MAAD about machine maintenance.
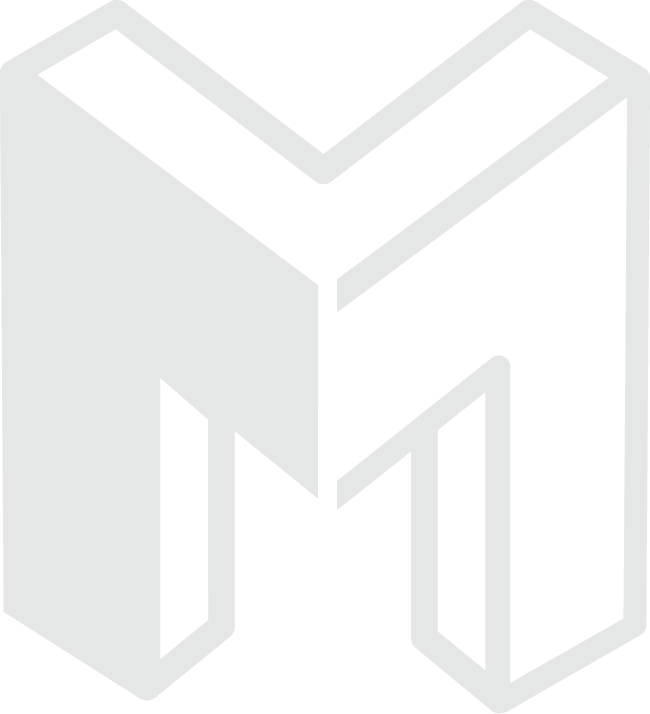
© Copyright 2022 MAAD